The
Arbori
Chair
The Arbori chair is the result of a two-month-long Scandinavian furniture design study abroad with the Danish Institute for Study-Abroad (DIS) in Copenhagen, Denmark, Summer 2023.
The flat-pack design enables cheap shipping and quick assembly.
Wood frame - washed scandinavian maple.
Cloth seating - 100% organic cotton unbleached canvas.
When sitting, you are cradled in cloth, not touching wood with any part of your body.
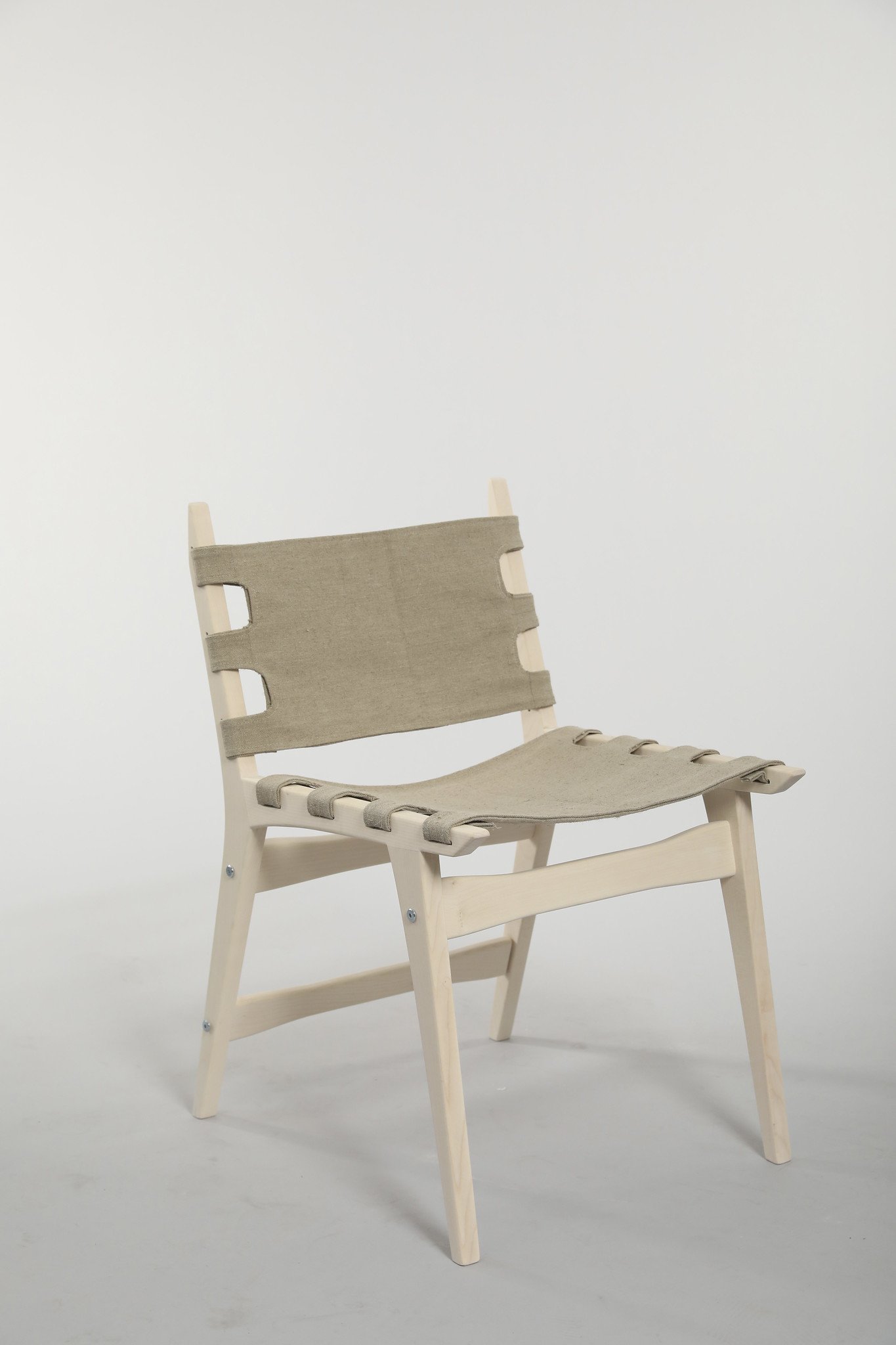

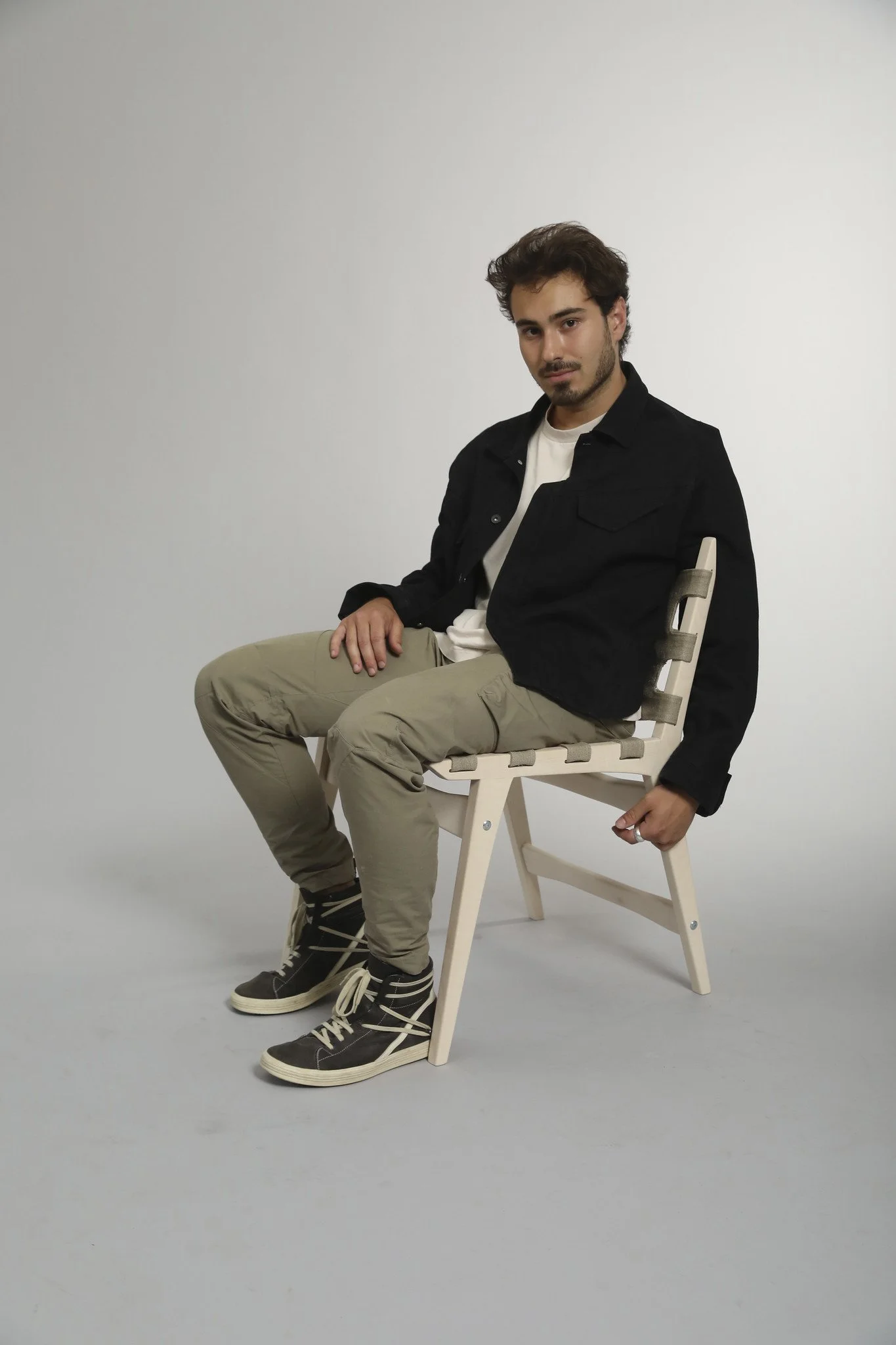
Process
1. Inspiration
•
2. Dreaming
•
3. Make It
•
4. Dream Bigger
•
5. Test It
•
6. Details
•
7. Putting In The Work
•
1. Inspiration • 2. Dreaming • 3. Make It • 4. Dream Bigger • 5. Test It • 6. Details • 7. Putting In The Work •
Step 1/7
Inspiration and Reserach
First, getting inspiration at some of the most beautiful furniture showrooms and manufacturers across Denmark, Sweden, and Finland.
Step 2/7
Dreaming
The initial sketches, where the Arbori chair first starts to take shape.
We only had 3 planks of wood to work with so I figured I should use the planks for a frame and cloth as the seat.
Step 3/7
Low Fidelity Miniature
Next, moving to miniature models of our sketches to bring 2D into 3D early in the process. Working in 3D helps to figure out the logistics of how things will connect together and will help problem solve in a different way than just 2D conceptualizations.
Step 4/7
Medium Fidelity Full Scale
Taking what we learned from mini-models, on to full scale drawings on trace paper. Here, I’m testing proportions and how things will actually fit together.
Step 5/7
Test it
After receiving a critique, we get back to work creating the full scale cardboard model. This is the first we can get a sense of the final product and how it interacts with the world around us. Objects give off a feeling and it’s hard to understand that feeling until it’s full scale.
Step 6/7
Details
Making any final decisions here, the working drawings which be used as “blueprints” during construction. As the chair is symmetrical i only need to draw 1 side view and half of the front and top view.
Step 7/7
Putting In The Work
Totalling ~50 hours across 2 weeks, I used the bandsaw spending the afternoons in design museums and exploring Copenhagen.
The back legs started with a slab of scandinavian maple ash that still had the bark on it, planed to thickness and cut out on the bandsaw. The rest of the pieces came from planks which underwent similar processing, but using the table saw to get the joinery angles perfect. I used a domino machine to create the negatives within the connections between the main pieces. The drill press was the best way to make the holes for the hardware. The wood was then finished up to 220 grit sandpaper and given soap washes in between sandings to give it a beautiful and traditional danish finish, celebrating the material, instead of altering it.
Finished
I’m ecstatic to have a physical manifestation of one of the most memorable summers of my life. I learned so much about woodworking, the tools associated, and the medium of wood itself
The chairs were exhibited at DIS the day after we finished making them. Immediately afterwards, we packed our chairs for shipping back to the US, luckily Arbori is flatpack capable and was brought on my flight home. Arbori was again exhibited for 3 months at the University of Colorado, Boulder in the Environmental Design building, along with other chairs from the DIS furniture design program.
I’m incredibly grateful for the opportunity and privilege I have for being able to partake in such an experience. I am most thankful for the welcoming teachers and mentors at DIS, the lovely friends I made through the experience, and most of all, to my mother who encouraged me to apply and is nothing but supportive for my creative endeavors.